Following a significant investment into JCB loaders last year, Copart recently visited the JCB World Headquarters to watch the latest models roll off the production line and collaborate on exciting new technology being developed to drive efficiencies and reduce carbon footprint.
In 2020, we made a substantial purchase of new JCB vehicle loaders as part of our ongoing investment into strengthening our logistical capabilities in line with growing customer demand, bringing Copart’s total owned UK wide logistics fleet to over 400.
As a tech-focused company that is committed to caring for the environment and encouraging sustainability in everything we do, our ongoing and close relationship with Watling JCB has proved to be a perfect partnership.
Always at the forefront of innovative and sustainable solutions, JCB are committed to making both their business and their machines more sustainable and have delivered many environmental initiatives in recent years.
During their visit to the JCB World Headquarters in Rocester, hosted by both JCB and JCB Watling, Copart UK’s Jane Pocock and Phil Briggs were able to see first-hand the amazing new technology being developed to help drive efficiencies, minimise environmental impact, and reduce carbon footprint.
With health and safety always top of our agenda, we have a stringent service and maintenance arrangement with Watling JCB, which utilises all the latest technology to keep our loaders in optimum condition.
Our loaders are monitored remotely by JCB, using by their JCB Livelink Telemetry System, which allows their service supervisors to access online information regarding machine health. Daily reports show the exact service status and location of each machine, and their engineers will attend Copart’s Operation Centres at the first sign of any potential issues.
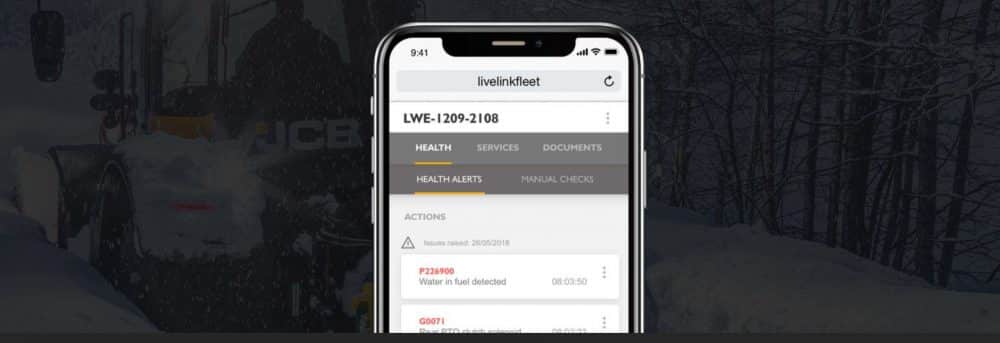
“Watling JCB provide a central service point of contact for Copart across the country and our service team has developed a great relationship across the Copart sites from three of our key depots.
Copart have a unique application and we have enjoyed working together to fine tune specification to best suit the requirements of the job, including increasing uptime, reducing admin, and enabling improved decision-making.”
Richard Barker, Sales Manager at Watling JCB.
Technology plays a major role in everything we do at Copart, and our fleet is no exception. With this in mind, we are working with Vision Track to install the same connected camera systems which have already been rolled out across out transporter fleet, to all our loaders.
These cameras will enable our managers to access live images, monitor activity in real time, and instantly retrieve footage if required. This helps to keep health and safety at the forefront our operations, whilst protecting our customers’ valuable assets.
And, with environmental values strongly aligned to our own, our relationship with JCB enables us to collaborate on the production of future build orders to ensure that we achieve our ‘greenest fleet on the street’ strategy.
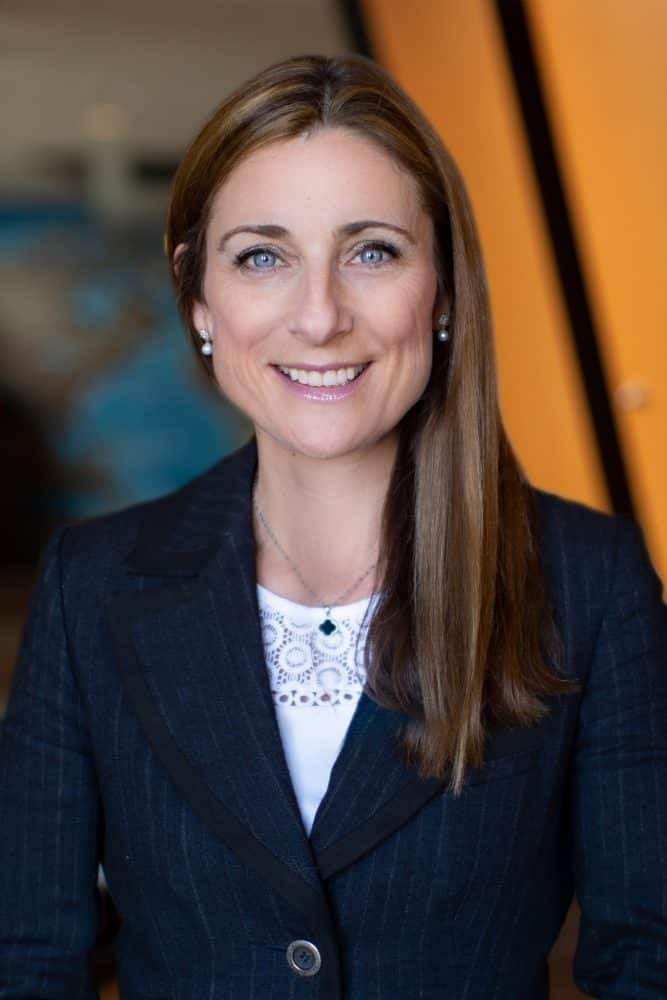
“Energy efficiency is a key focus for JCB, and they have now launched their first fully electric machines alongside the continued pursuit of cleaner diesel engine technology.
At Copart, we are committed to minimising environmental impact in everything we do, so we’re very excited about collaborating with JCB on orders for future vehicle loaders and exploring lower emission options including alternative fuels and renewable energy.”
Jane Pocock – Managing Director of Copart UK & Ireland
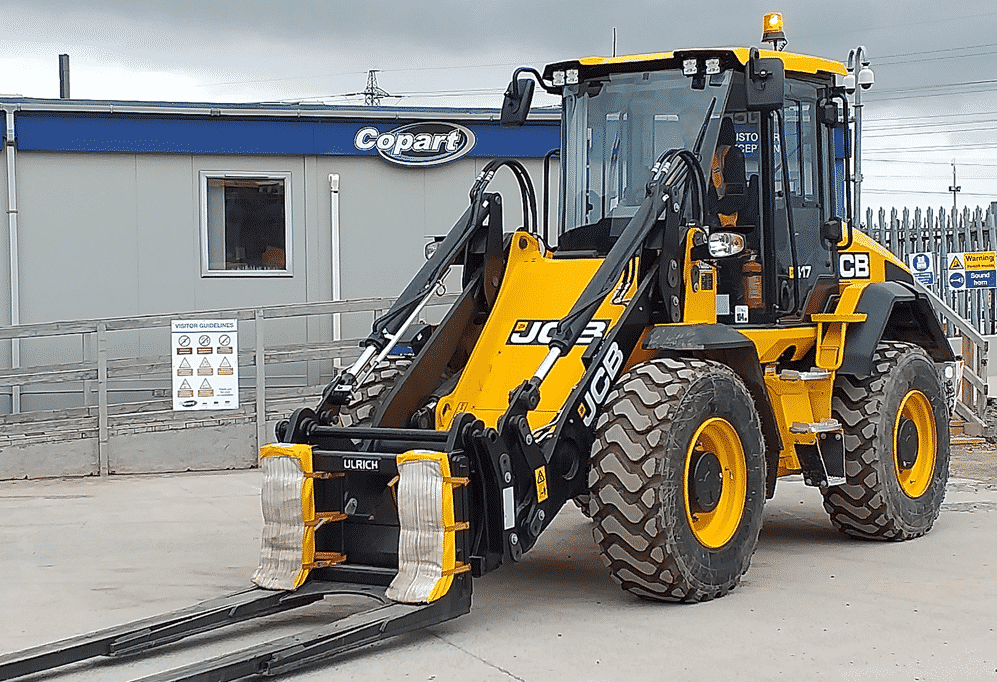
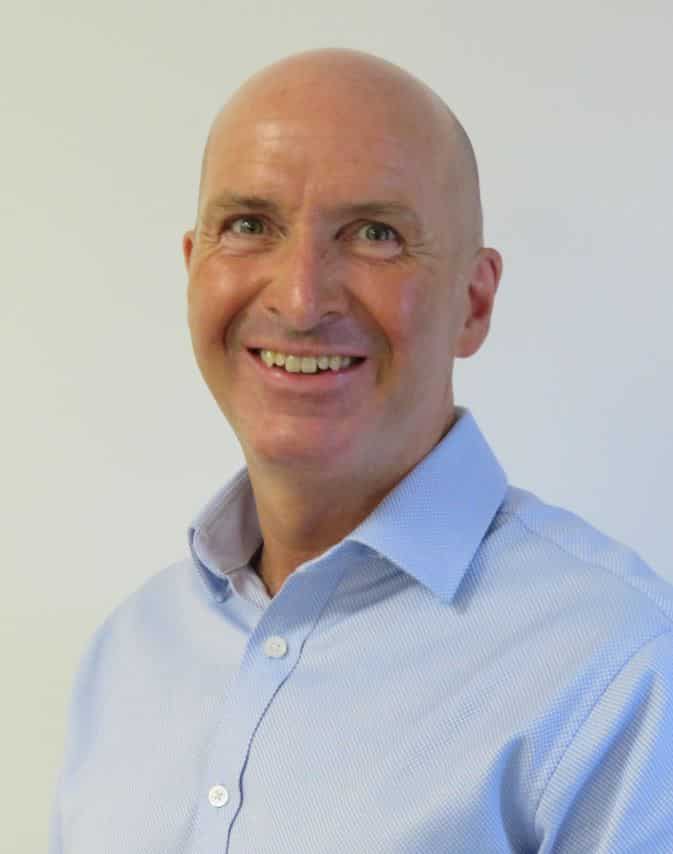
“Our continued investment into new JCB loaders, which are critical for safely moving our customers’ vehicles, enables us to handle increasing volumes and supports our future needs as acquire new land and develop existing Operation Centres.
Our relationship with JCB is key to future-proofing our logistics fleet to ensure that it is both efficient and environmentally friendly.”
Phil Briggs – Director of Operation Centres, Transport & Engineering